與普通熱固性塑料一樣,BMC的成型技術(shù)包括模壓成型、傳遞成型和注射成型。但實(shí)際上很長(zhǎng)時(shí)間里多數(shù)場(chǎng)合下BMC通常以模壓成型和注射成型為主。近幾年來(lái),BMC注射成型技術(shù)已開(kāi)始用于對(duì)強(qiáng)度要求較高的大型制品的快速生產(chǎn)。灌注成型工藝是一種新的成型工藝,它采用的原材料類似于模壓成型工藝和注射成型工藝的[4]。
2.1BMC模壓成型工藝
2.1.1模壓成型的優(yōu)缺點(diǎn):
模壓成型工藝是復(fù)合材料生產(chǎn)中最古老而又富有無(wú)限活力的一種成型方法。它是將一定量的預(yù)混料或預(yù)浸料加入金屬對(duì)模內(nèi),經(jīng)加熱、加壓固化成型的方法[17~18]。
模壓成型工藝的主要優(yōu)點(diǎn):
①生產(chǎn)效率高,便于實(shí)現(xiàn)專業(yè)化和自動(dòng)化生產(chǎn);
②產(chǎn)品尺寸精度高,重復(fù)性好;
③表面光潔,無(wú)需二次修飾;
④能一次成型結(jié)構(gòu)復(fù)雜的制品;
⑤因?yàn)榕可a(chǎn),價(jià)格相對(duì)低廉。
模壓成型的不足之處在于模具制造復(fù)雜,投資較大,加上受壓機(jī)限制,最適合于批量生產(chǎn)中小型復(fù)合材料制品。隨著金屬加工技術(shù)、壓機(jī)制造水平及合成樹(shù)脂工藝性能的不斷改進(jìn)和發(fā)展,壓機(jī)噸位和臺(tái)面尺寸不斷增大,模壓料的成型溫度和壓力也相對(duì)降低,使得模壓成型制品的尺寸逐步向大型化發(fā)展,目前已能生產(chǎn)大型汽車部件、浴盆、整體衛(wèi)生間組件等[28]。
2.1.2模壓成型工藝過(guò)程
(1)物料的準(zhǔn)備與加料
BMC一般有兩種形態(tài),一類為塊(團(tuán))狀模塑料(塊狀BMC),一類為散狀模塑料(散狀BMC)。一般在BMC生產(chǎn)的最后階段,為了便于處理和以后的操作,通常都有一專門的設(shè)備擠壓成繩條狀、木節(jié)狀或彈丸狀。而當(dāng)BMC配方中纖維含量較高時(shí),其松散性也增加。很難做成致密的規(guī)則形狀,這類材料一般都采用人工稱量加料。而對(duì)于擠壓成的塊狀模塑料則可以實(shí)現(xiàn)比較準(zhǔn)確的、方便的甚至是自動(dòng)化的加料方式。但是,使用擠壓料坯時(shí)應(yīng)注意到混合物的緊密壓縮會(huì)降低其貯存壽命。這一點(diǎn)可能與松散的BMC內(nèi)夾雜空氣,抑制其聚合反應(yīng)有關(guān)。同時(shí),空氣也可以帶走料團(tuán)內(nèi)部少量之聚合熱[6]。
散狀BMC,由于體積比較大,需采用具有較大裝料室的模具。散狀材料中易滯留空氣,容易在成型制品中出現(xiàn)多孔區(qū)或氣泡。為防止這類瑕疵的出現(xiàn),可用手預(yù)先擠壓料團(tuán),使其成一定形狀(如球形等)。
BMC在模腔內(nèi)的放置位置,最好應(yīng)保證在壓膜閉合時(shí),料流能同時(shí)到達(dá)模腔的各個(gè)角落。否則,料流必須從側(cè)面流動(dòng),使制品產(chǎn)生裂紋、填充不良和其他缺陷。在成型孔洞的周圍產(chǎn)生熔接線,造成制品局部強(qiáng)度下降。
由于手工稱量速度相當(dāng)慢,不利于提高生產(chǎn)效率。在小制品成型時(shí),可以使多個(gè)成型件使用公用成型腔,這樣僅用一塊物料就可以同時(shí)成型多個(gè)制品。
形狀復(fù)雜的制品,可預(yù)先按制品形狀壓成坯塊,然后再成型,這樣可以預(yù)防各凸出部分產(chǎn)生尺寸誤差,并且不至于產(chǎn)生熔接線等缺點(diǎn)。但是,對(duì)于某些玻璃含量高的BMC,難以用機(jī)械法壓制料坯,因?yàn)橛脵C(jī)械法需要產(chǎn)生足夠的壓縮才能形成料坯,而聚酯料塊有時(shí)很粘,難以從坯模上取出。
采用繩條形狀的BMC模壓制品時(shí),應(yīng)采用垂直加料的方式,以便使制品各方向之強(qiáng)度一致和收縮一致。同時(shí)每一制品只宜放置一個(gè)質(zhì)量與制品相同的料團(tuán),如使用多個(gè)料團(tuán),則料團(tuán)間的流動(dòng)匯集點(diǎn)會(huì)形成明顯的熔接線,該區(qū)的強(qiáng)度大大低于制品的其他部分。
(2)成型工藝參數(shù)的選擇
由于BMC具有良好的流動(dòng)性,固化過(guò)程中又無(wú)揮發(fā)物產(chǎn)生,因而不需使用很高的成型壓力就可使物料充滿模腔,完成固化過(guò)程。對(duì)某些結(jié)構(gòu)簡(jiǎn)單的制品,只需0.7Mpa的壓力就可成型,但是一般采用的成型壓力范圍3.5~14Mpa。使用較高的成型壓力對(duì)加快成型速度有一定的好處,它可使多余的物料溢出,并產(chǎn)生精確的、填充良好的制品。但壓力過(guò)高有時(shí)也會(huì)因溢料嚴(yán)重而造成脫模困難,某些配方,壓力過(guò)高,還會(huì)引起粘模。
BMC的成型溫度一般為110~170℃,成型溫度的高低與BMC的固化速度、制品的復(fù)雜程度、收縮控制、流動(dòng)條件等有關(guān)。欲快速固化可提高成型溫度,如制品形狀復(fù)雜,為保證料流有足夠的時(shí)間充滿模腔的各個(gè)角落,成型溫度宜低些。有時(shí)為了使制品選擇性粘模,可調(diào)正上、下模溫差,但一般不超過(guò)10℃。
制品的固化時(shí)間與物料的固化速度有關(guān),也與制品厚度。成型溫度有關(guān)。制品越厚,則所需的固化時(shí)間越長(zhǎng)。扁平制品,一般要在模具內(nèi)實(shí)現(xiàn)充分的固化。但是,一般制品為縮短在壓機(jī)模具組合內(nèi)的時(shí)間,經(jīng)常采用后處理工藝[7]。
通用型和低收縮型BMC的典型工藝參數(shù)是:
成型壓力 3.5~7Mpa
成型溫度 132~177℃
保溫時(shí)間 45s
(3)脫模
當(dāng)制品完全固化后,可以脫模。
2.2BMC注射成型工藝
2.2.1注射成型特點(diǎn)
注射成型與模壓成型相比較,它的成型周期比模壓成型短且質(zhì)量也更好,成本也低。主要原因在于它在注射成型過(guò)程中,BMC料在模具內(nèi)可以有效的分配,它可以使用多槽模具,不用像模壓成型那樣去花費(fèi)很大精力在稱量和在加料上。但是BMC注射成型制品的強(qiáng)度通常情況下沒(méi)有模壓成型制品的強(qiáng)度高[26]。
2.2.2注射成型工藝過(guò)程
BMC經(jīng)料斗進(jìn)入具有一定溫度的料筒中受熱軟化,并隨料筒溫度的升高 和螺桿旋轉(zhuǎn)或柱塞推進(jìn)而不并斷受到剪切,且與料筒壁摩擦生熱而使BMC進(jìn)一步塑化成粘流狀態(tài),然后在螺桿或柱塞的推動(dòng)不經(jīng)噴嘴和流道注射進(jìn)高溫模具中,粘度急劇增加,經(jīng)適當(dāng)時(shí)間的保溫、固化,開(kāi)模取件。從BMC人料筒至出料筒過(guò)程中,BMC在發(fā)生物理變化的同時(shí)又發(fā)生緩慢的化學(xué)變化。而從噴嘴注入高溫模腔后,則發(fā)生固化反應(yīng),形成玻纖增強(qiáng),填料填充的網(wǎng)狀體型結(jié)構(gòu)。
BMC注射成型的基本工藝過(guò)程:(1)加料,料筒中必須充滿BMC;(2)合模;(3)注射;(4)保壓,保溫固化;(5)開(kāi)模;(6)取件。
2.2.3BMC制品強(qiáng)度影響因素
為使BMC注射成型有更高的效率和更好的產(chǎn)品質(zhì)量理想的強(qiáng)度,一方面必須在生產(chǎn)過(guò)程中嚴(yán)格控制3個(gè)重要參數(shù):注射壓力,注射時(shí)間和模具溫度。另一方面,對(duì)原材料也要有特殊的要求,如玻璃纖維的破損,玻璃纖維的取向和樹(shù)脂的分類。
注射成型條件控制:
BMC通常僅需要非常低的注射壓力,一般范圍為28~35MPa料筒的溫度要盡可能保持得低一點(diǎn),一般控制在20~60℃范圍內(nèi)。而模具壓力溫度要高一點(diǎn),一般控制在135~160℃。注射速度控制在1~7/s。操作條件控制不好會(huì)影響制品的機(jī)械性能,注射速度越快,纖維取向更為嚴(yán)重,玻璃纖維的破損也在一定程度上與注射速度有關(guān)。
注射機(jī)和模具設(shè)計(jì)對(duì)注射成型產(chǎn)品的影響:
(1)注射機(jī)對(duì)注射成型產(chǎn)品的影響
注射機(jī)主要有螺桿式注射機(jī)和柱塞式注射機(jī)。柱塞式注射機(jī)對(duì)纖維的機(jī)械損傷小,但是空氣不易排出,所以它的產(chǎn)品外觀質(zhì)量不如螺桿式注射機(jī)的制品。螺桿式注射機(jī)成型效率高,制品質(zhì)量好,但是它對(duì)纖維的機(jī)械損傷比較大[23]。
(2)模具設(shè)計(jì)對(duì)注射成型產(chǎn)品的影響[5]
BMC材料強(qiáng)度主要在注口和流道中受到損傷,所以,在布局設(shè)計(jì)的時(shí)候應(yīng)特別注意注口和流道的設(shè)計(jì)。澆口和流道對(duì)BMC制品的強(qiáng)度影響如下:
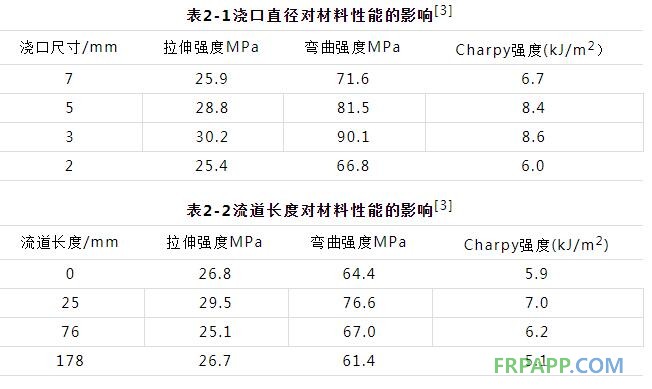
從表2-1和2-2兩張表可以看出:澆口尺寸從2mm變化到7mm時(shí),機(jī)械性能都上升;流道長(zhǎng)度從0mm變化到178mm時(shí),機(jī)械性能性能下降。所以說(shuō),澆口直徑越大,流道長(zhǎng)度越短,對(duì)纖維的機(jī)械損傷越小,纖維就越完整。
2.3BMC灌注成型工藝
BMC采用的原材料有不飽和聚酯樹(shù)脂、填料、玻璃纖維、增稠劑等增稠劑。不飽和聚酯樹(shù)脂中,選用苯乙烯單體用作不飽和聚酯樹(shù)脂的單體交聯(lián)劑、活性稀釋劑,用量一般為30%~40%。填料選用碳酸鈣。玻璃纖維選用短切玻璃纖維(6mm左右)[25]。
BMC灌注成型工藝類似于模壓成型,它不需要二次加熱。將不飽和聚酯樹(shù)脂、填料、固化劑和其他添加劑混合,制成樹(shù)脂糊,再將樹(shù)脂糊與短切玻璃纖維混合,進(jìn)行充分、均勻的攪拌[26]。如果攪拌不均勻會(huì)導(dǎo)致玻璃纖維沉積,制品的強(qiáng)度不均勻,局部強(qiáng)度過(guò)低。然后將樹(shù)脂糊與玻璃纖維的混合料倒入模具中,應(yīng)保證在壓膜閉合時(shí),料流能同時(shí)到達(dá)模腔的各個(gè)角落,閉合模具,進(jìn)行固化。主要成型參數(shù):成型壓力:3.5~7MPa;成型溫度132~177℃;保溫時(shí)間:45s[21]。
等制品固化完成后,即可開(kāi)始脫模。由于BMC制品中加入內(nèi)脫模劑,開(kāi)模后,制品容易取出。