日前,美國Bonded Composite公司開發(fā)的復(fù)合材料機(jī)身結(jié)構(gòu)展示了一種更經(jīng)濟(jì)的檢測技術(shù),完全能夠滿足美國空軍增加航程、降低燃油消耗的目標(biāo)要求。
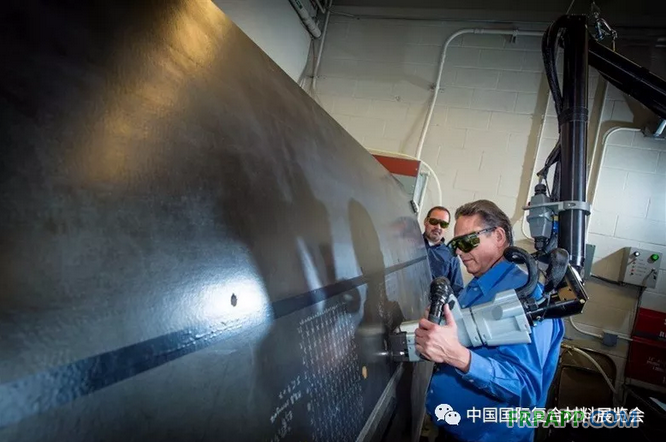
激光粘接檢驗(yàn)(Laser bond inspection,LBI)與粘接過程控制相結(jié)合能夠顯著促進(jìn)并實(shí)現(xiàn)一級粘接復(fù)合材料結(jié)構(gòu)件的技術(shù)轉(zhuǎn)化。
復(fù)合材料結(jié)構(gòu),使用粘接劑連接,而非傳統(tǒng)的鉚釘或緊固件連接,因此,需要一種新的檢測方法來驗(yàn)證復(fù)合材料連接的強(qiáng)度和安全性。
LBI是一種通過探測由高能脈沖激光激發(fā)的應(yīng)力波來查驗(yàn)不合格連接的無損檢測手段。
一個微小的連接缺陷將在脈沖探測時破裂,而一個合格的標(biāo)準(zhǔn)連接則將在脈沖激勵后保持不變。不合格的粘接缺陷可能是由于膠粘劑混合不勻、表面處理不當(dāng)或雜質(zhì)造成的。
LBI是唯一一種可靠且成熟的評價復(fù)合材料結(jié)構(gòu)粘接完整性、檢測弱結(jié)合缺陷(兩個表面能緊密接觸,但沒有正確結(jié)合的粘合線缺陷)的檢測方法。
美國空軍研究實(shí)驗(yàn)室(AFRL)材料和制造局結(jié)構(gòu)組主管Andrea Heldrea表示:“這項(xiàng)技術(shù)成果凝聚了包括美國空軍、波音公司、LSP技術(shù)公司以及主要的航空航天原設(shè)備制造商超過10年的通力合作和研究開發(fā)。然而,研究遠(yuǎn)沒有結(jié)束。目前,研究主要是在多個典型飛機(jī)結(jié)構(gòu)件和原型光纖傳輸系統(tǒng)中對該技術(shù)進(jìn)行驗(yàn)證,以擴(kuò)大其使用范圍。”
該領(lǐng)域下一步的研究包括復(fù)合材料粘接一體化技術(shù)的數(shù)據(jù)分析。同時,需要通過測試來定義更多材料、厚度和連接設(shè)計,從而更好的將該技術(shù)平臺推廣到其他領(lǐng)域。另外,激光粘接檢驗(yàn)單元也需要進(jìn)行硬件升級,以提高生產(chǎn)條件下的可用性。
該技術(shù)與美國國防高級研究計劃署的一個粘接過程控制研究項(xiàng)目都是在航空航天領(lǐng)域啟用粘接復(fù)合材料結(jié)構(gòu)件的關(guān)鍵步驟。
而要獲得節(jié)省制造周期、擴(kuò)大該技術(shù)應(yīng)用機(jī)型范圍的新方法則需面臨更大的挑戰(zhàn)。LBI使粘接復(fù)合材料結(jié)構(gòu)件的應(yīng)用成為可能,這是該領(lǐng)域技術(shù)在正確前進(jìn)方向上邁出的一大步。