零部件的每一克重量對(duì)電動(dòng)跑車而言都尤為關(guān)鍵,為此,首款采用全塑制動(dòng)踏板的量產(chǎn)跑車應(yīng)運(yùn)而生。這一安全部件由朗盛高性能材料(HPM)業(yè)務(wù)部與國(guó)際供應(yīng)商BOGEElastmetall聯(lián)合開(kāi)發(fā),該公司主要為汽車行業(yè)提供減振系統(tǒng)和塑料部件。
這款制動(dòng)踏板采用熱塑性復(fù)合結(jié)構(gòu),使其達(dá)到極佳機(jī)械性能的同時(shí)保持輕量化。其結(jié)構(gòu)包括由朗盛Tepexdynalite,一種連續(xù)纖維增強(qiáng)熱塑性復(fù)合材料制成的嵌件,并搭配多組加強(qiáng)筋。
Tepex嵌件的定制纖維結(jié)構(gòu)搭配多層嵌條加強(qiáng),這一復(fù)合結(jié)構(gòu)使得該制動(dòng)踏板比同類鋼制產(chǎn)品輕50%,又滿足較高的負(fù)載要求。自動(dòng)化操作使這一形狀不規(guī)則的安全部件得以高效、批量生產(chǎn)。”
朗盛高性能材料(HPM)業(yè)務(wù)部Tepex汽車集團(tuán)輕質(zhì)結(jié)構(gòu)專家KlausVonberg博士介紹道。
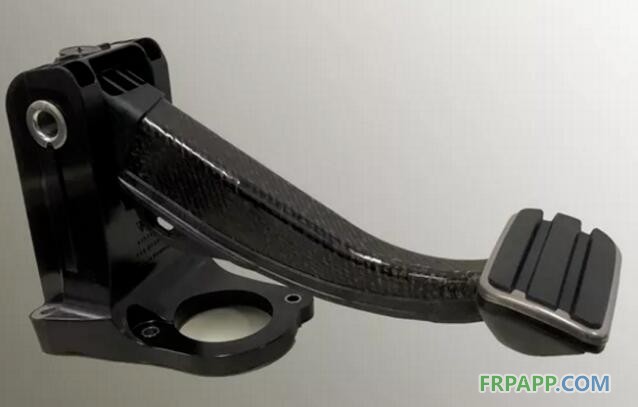
全塑制動(dòng)踏板,用于蓄電池電動(dòng)跑車,其結(jié)構(gòu)包括由朗盛Tepex dynalite,一款連續(xù)纖維增強(qiáng)熱塑性復(fù)合材料制成的鑲塊。
照片:朗盛化學(xué)
精確組合多向排列的纖維層
Tepexdynalite是一種完全整合的半成品,其熱塑性基體材料通常由多層連續(xù)玻璃纖維加強(qiáng)。電動(dòng)跑車的制動(dòng)踏板采用聚酰胺6基體復(fù)合結(jié)構(gòu),該復(fù)合結(jié)構(gòu)的內(nèi)層為單向的纖維層,外覆多層45°排列的纖維編織層,其中內(nèi)層是實(shí)現(xiàn)踏板高抗彎、抗扭的關(guān)鍵。
肋條是較薄的塑料條,由單向排列的高強(qiáng)度連續(xù)纖維構(gòu)成,用于嵌入熱塑性基體。制動(dòng)踏板的底部采用多層嵌條和玻璃纖維粗紗加固。
由于嵌條的塑料基體可與Tepex鑲塊的兼容,簡(jiǎn)單通過(guò)激光即可完成焊接,使得這一定制的纖維層壓板可以遵循精確的負(fù)載路徑,適應(yīng)特定負(fù)載部件的要求。鑲塊45°排列的纖維外覆層與頂部的嵌條相結(jié)合,確保踏板的高抗扭強(qiáng)度。
批量生產(chǎn)四款制動(dòng)踏板
“這一定制的纖維層結(jié)構(gòu),搭配有機(jī)片材和肋條,使制動(dòng)踏板有望進(jìn)一步減重,同時(shí)實(shí)現(xiàn)其需要達(dá)到的卓越機(jī)械性能。”
BOGEElastmetall創(chuàng)新中心的DanielH?ffelin博士說(shuō)道。
現(xiàn)有四款不同設(shè)計(jì)的全塑制動(dòng)踏板投入批量生產(chǎn),其負(fù)載路徑均已優(yōu)化,以應(yīng)對(duì)不同扭轉(zhuǎn)方向。
一次成型嵌條與Tepex
制動(dòng)踏板采用一次混合成型工藝制造,周期短,適合大規(guī)模批量化生產(chǎn)。
該工藝整合了Tepex嵌件和肋條的后續(xù)覆合工序。生產(chǎn)的第一步是借助光學(xué)測(cè)量系統(tǒng),精確校準(zhǔn)嵌條在Tepex嵌件上的位置,以便焊接。這一步通過(guò)熱塑成型,然后再用聚酰胺66反向注塑成型。
電動(dòng)汽車的高強(qiáng)度結(jié)構(gòu)部件
熱塑性復(fù)合結(jié)構(gòu)與定向纖維的組合,為電動(dòng)汽車領(lǐng)域帶來(lái)新機(jī)遇。
Vonberg博士表示:“Tepex鑲塊可用于前端支架和保險(xiǎn)杠、電氣和電子模塊支架、行李箱和備用輪艙、蓄電池罩、車輛“溫室”部分的結(jié)構(gòu)組件以及車身下方電池的保護(hù)結(jié)構(gòu)。”
相對(duì)于金屬結(jié)構(gòu)的部件,低碳足跡也是采用Tepex與嵌條復(fù)合結(jié)構(gòu)的原因之一。熱塑性復(fù)合材料不僅比同類材料更輕巧,其采用的混合成型工藝也更減重節(jié)能、節(jié)省成本,因?yàn)樵摴に噷?dǎo)向、支架和緊固件等工序融為一體。使用熱塑性復(fù)合材料,就無(wú)需再耗時(shí)完成進(jìn)一步加工,如拋光或后續(xù)出鋼等金屬部件的常規(guī)步驟。